Our Process

Production
The Harlan family has a long heritage of farming, dating back to 1852. Given our Yolo County origin, tomatoes serve as our primary crop; hay and cereal grains have historically served as a crop rotation. In recent years we have expanded our acreage to meet consumer demand for a year round, high quality hay product. Today our combined acreage of alfalfa and oats is about 2,500 acres. As we have become more vested in the hay market, we felt that developing methods of directly marketing our hay products was a natural complement to our business.
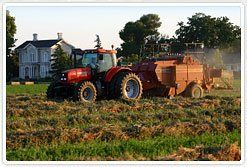
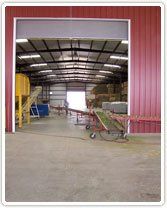
Being the producers of the feed we process has many advantages. We are able to direct not only the field quality, but the quality of product going into the mill. All alfalfa hay is field tested for total digestive nutrients (TDN) and protein. High TDN and protein (test hay), alfalfa from grassy fields, and hay that has encountered weather damage is re-directed to non-horse markets. Adequate warehouse storage has been added to supply our customers with product year round.
Preventing hay exposure to elements such as adverse weather and moisture ensures a high quality feed and ultimately is of value to the customer. Therefore the entire milling process is on a concrete platform and under a bay that is connected to the warehouse. From bale, to cube, to delivery our products are protected from the elements.
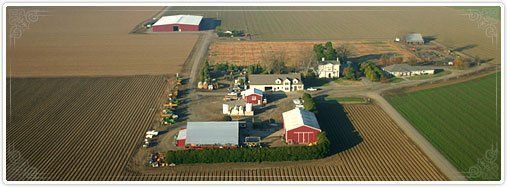
We run a Warren & Baerg Model 250 in-line, industrial cuber. In-line refers to our ability to place bales on a moving, elevated chain into the knife assembly. One advantage of this system is that the bales are individually placed into the mill, allowing a final inspection. We then stack ingredients on top of the large bales (such as oat hay or corn). By placing the ingredients on the top of the bales, both the alfalfa and secondary ingredients enter the knifing assembly simultaneously yielding a consistent and uniform blend of product. The mixed product passes through a series of magnets, which remove any foreign metallic pieces.
Processing
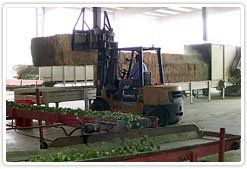
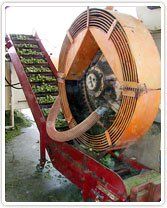
A fine mist of fresh water is then added to the mixture as it enters a large press wheel. This ensures proper binding. The hay is compressed into a square die until it hits and is broken by a deflector shield.
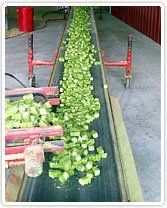
From the deflector shield the cubes fall onto a chain belt, this allows for the separation of the fines from the cube product. At this time, the cubes are about 140 degrees. To remove added moisture and return the product to an ambient temperature for storage, the product slowly passes through an evaporator.
From here the product travels by belt to bulk storage, to be shipped to customers in bulk or to be weighed and filled into 50 pound sacks.
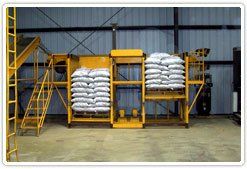
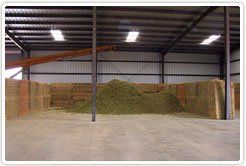